COSMHYC XL Project Learn more about
you are here: Learn more about
COSMHYC XL Project - Innovative compression solutions for efficient hydrogen mobility.
Learn more about
H2 production and benefits
Hydrogen is the simplest and most abundant element in the universe, but its gaseous form H2 doesn't occur naturally. H2 can be produced through different processes: reforming of natural gas, gasification of heavy fossil fuels, or water electrolysis. All are mature technologies applied on a large scale, mostly in industrial applications.
Electrolysis, a process of splitting water into hydrogen and oxygen by applying a direct current, can produce hydrogen directly from renewable electricity, providing a way to store it in chemical form.
The need for energy storage is becoming more acute with the increase of intermittent renewable electricity generation from wind and solar, which is not aligned with grid power demand. Water electrolysis technology is currently the most flexible solution for storing renewable electricity on a large scale in the form of H2.
When produced by electrolysis with electricity from renewable sources:
- H2 allows storing low-carbon energy
- H2 facilitates the integration of high shares of intermittently generated renewable electricity in energy systems
- H2 is an option for increasing the flexibility of the energy system
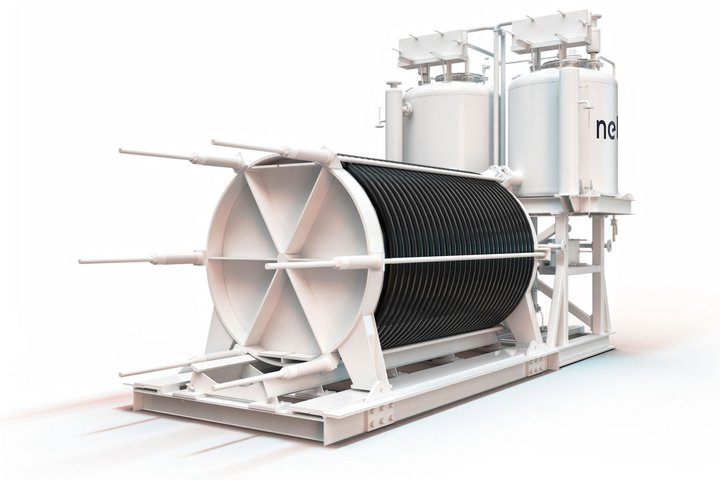
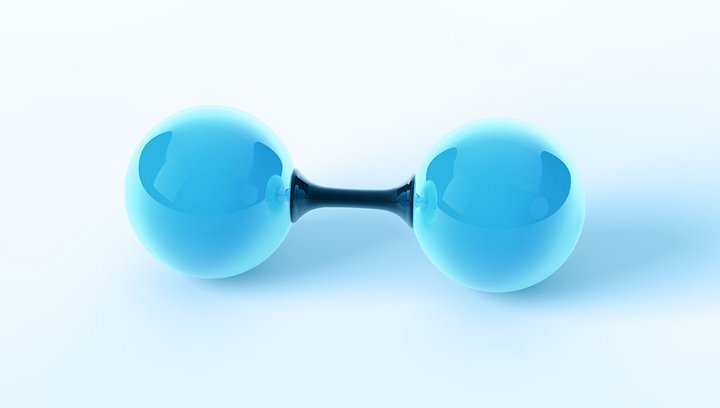
Learn more about
fuel cell electric vehicles
In a fuel cell, a hydrogen-rich fuel is oxidized and converted into heat and electricity. If pure hydrogen is used, the exhaust of fuel cells is only water vapour.
Fuel cells can be used for road passenger vehicles but also for industrial fleets and material handling vehicles, rail and air transport as well as for shipping, river navigation and pleasure boating. In Fuel Cell Electric Vehicles (FCEVs) powered by H2, the electricity needed for the engine is produced without any local pollutants emissions, eliminating local environmental and health impacts otherwise caused by transport. When H2 produced from renewables is used, overall CO2 emissions are significantly reduced and FCEVs are a low-carbon alternative to conventional transport.
The transport sector needs carbon-free solutions. A range of technical options are currently under development or are being introduced to the market: battery electric vehicles, plug-in hybrid vehicles, FCEVs or even industrial and commercial vehicles using liquid or gaseous hydrocarbon fuels synthesized from renewable hydrogen. A combination of these options is required to meet the different mobility needs of society and individuals. H2 mobility, alongside with battery technology, is thus part of the solution to fight climate change.
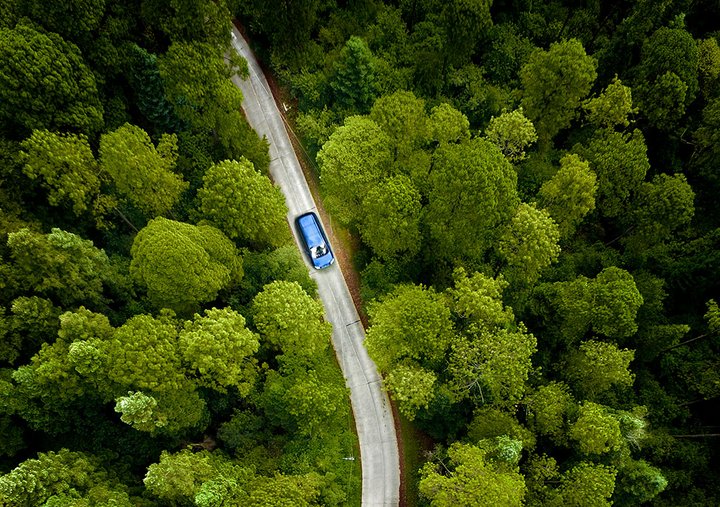
Learn more about
Infrastructure for H2 Mobility
The on-road practicability of FCEVs has been demonstrated. Moreover, hydrogen cars are silent and comfortable. By the end of 2016, about 5,000 FCEVs were on the roads all over the world. At present, manufacturers start the production of affordable FCEVs in series. Well-developed infrastructures and efficient technologies for hydrogen refuelling stations are key to FCEVs market deployment.
The transport and distribution infrastructure can be composed of different elements depending on where the hydrogen is produced:
- On-site production (or near the refuelling station): the electrolyser has to be installed and access to a sufficient amount of renewable electricity has to be ensured.
- Off-site production: hydrogen needs to be compressed, pumped into the storage vessels (e.g., compressed hydrogen tube trailers or liquid hydrogen trailers) and transported (pipelines or trucks).
- Storage solutions to ensure the availablitity of hydrogen.
- Compressors are needed to supply high-pressure hydrogen to the FCEVs´ tanks.
- Refuelling station for the distribution and the sale of the hydrogen fuel.
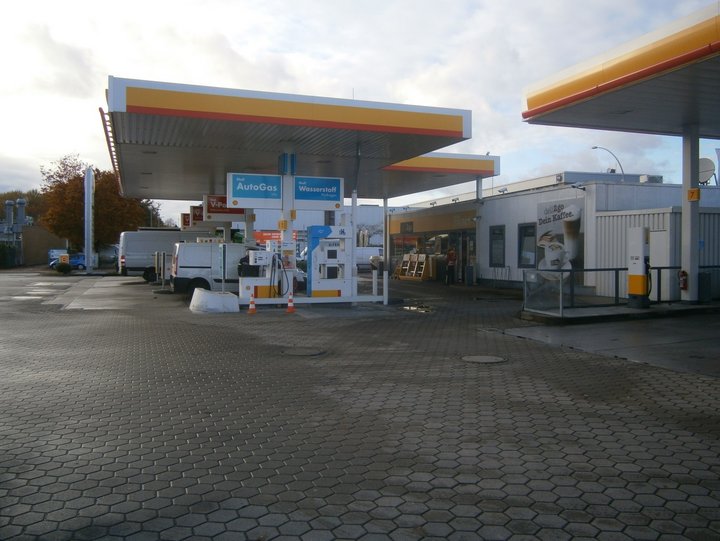
Learn more about
hydrogen refuelling stations
With the market entry of serial production FCEVs, national hydrogen refuelling station networks are currently starting to grow in many EU countries. FCEVs can be refuelled in 3 to 5 minutes, thereby offering refuelling times similar to those of conventional cars. The refuelling stations can be dedicated to hydrogen refuelling or can be part of a multi-fuel station.
FCEV drivers should be able to refuel their vehicles when and wherever they need to. A hydrogen refuelling station network that lives up to this promise is starting to emergy in several European countries. A minimum coverage is a prerequisite for increased usage of hydrogen vehicles. Refuelling stations should be located at the right places! Clustering them around demand centres and connecting corridors is an option to provide coverage at minimal costs and with maximum effect.
The optimal size of a station is another critical element and is largely determined by daily hydrogen demand. New generation fuelling devices are now entering the market, enabling hydrogen supply even at rush-hours. These devices are compact, saving space within the station and the storage capacity can be dimensioned to address different demand and supply configurations.
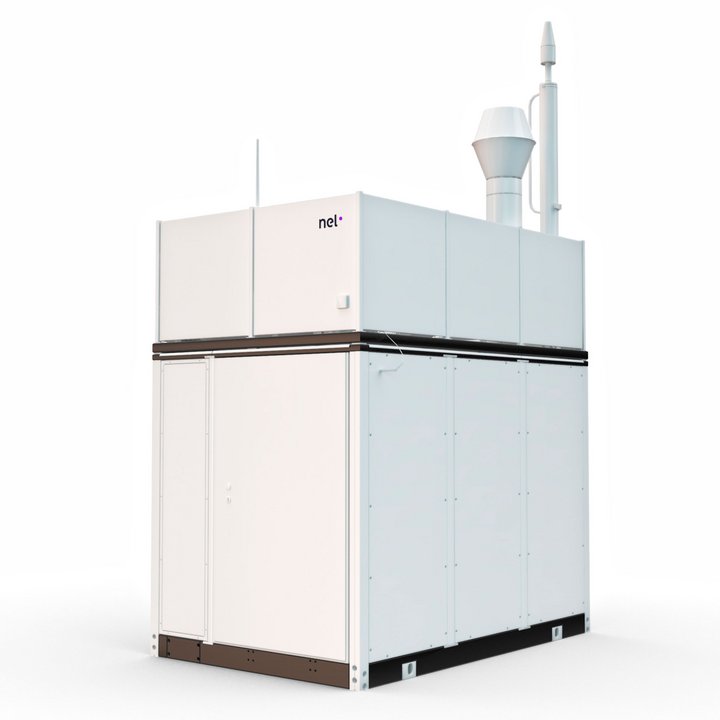
Learn more about
H2 compression
Hydrogen is usually produced at low pressure (10 to 50 bar), but then must be compressed before transportation or distribution (350 to 700 bar for FCEVs). There are different technologies to compress hydrogen, most of them involving mechanical compression.
Below are some of the different types of compressors:
- Reciprocating compressors use an engine to move back and forth a piston or a diaphragm. This method is widely used. By moving this piston, hydrogen is confined into a smaller volume and therefore mechanically compressed.
- Rotary compression uses the rotation of screws, gears, etc. to force more gas into a given volume.
- Centrifugal compressors are equipped with a turbine that rotates at a very high speed to compress H2
Alternatives technologies are also available to limit the electrical consumption and the noise and heat production, while reducing CAPEX and OPEX costs.
One of the most promising ones is the use of metal hydrides. Hydrogen is absorbed into a metallic powder at a certain pressure and can be released at a higher pressure thanks to an increase of temperature.
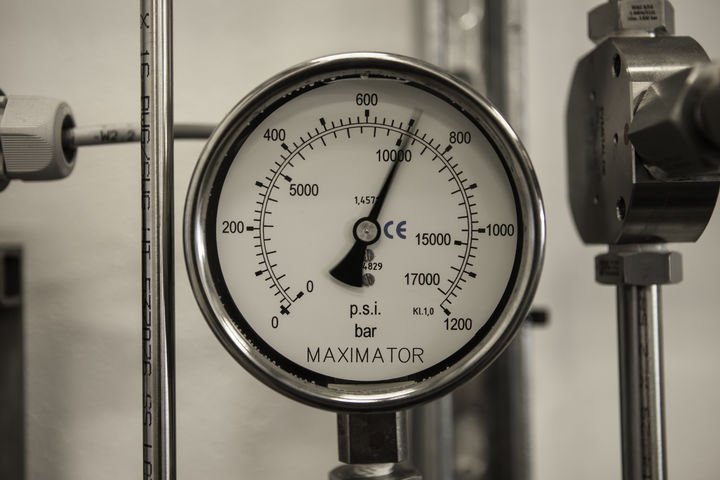
Learn More About
Metal Hydrides
Metal hydrides are binary compounds formed by hydrogen and another metal element (e.g., alloys). These chemical connections are one way to store hydrogen in a compact way.
In metal hydrides, hydrogen is stored in a reversible way meaning that hydrogen is released again from the metal when it needs to be used.
Metal hydrides store hydrogen in solid form under moderate temperature and pressure. Increasing the temperature enables to release again hydrogen from the metal and reach higher pressure.
Different metals react differently with hydrogen. Thus, it is crucial to optimally modify the composition of the hydrides, so that these chemical combinations can be used at their best.

Learn more about
Metal Hydride Compression
Metal hydride compression is driven by a chemical process. The main principle of metal hydride compression utilizes a reversible, heat driven interaction between the hydride-forming metal alloy, and hydrogen gas, to form a metal hydride.
When hydrogen is absorbed in the metal alloy at a low temperature and a low pressure, the fact to provide heat at a higher temperature enables to release the hydrogen at a higher pressure, producing a compression effect.
The relationship between the temperature of the heat source and the release pressure of the hydrogen in the desorption phase depends on the metal alloy. By combining different metal alloys in different compression stages, it is possible to reach overall pressures of 1000 bar or more. The main challenge for this compression technology is to find the right alloy to optimise the process, by maximising the amount of hydride absorbed in the metal hydrides while minimising the energy needed for the whole compression cycle (i.e. absorption, heating, desorption and cooling).
Benefits of using a hydride compression system:
- no moving parts needed
- low maintenance costs
- little wear and tear
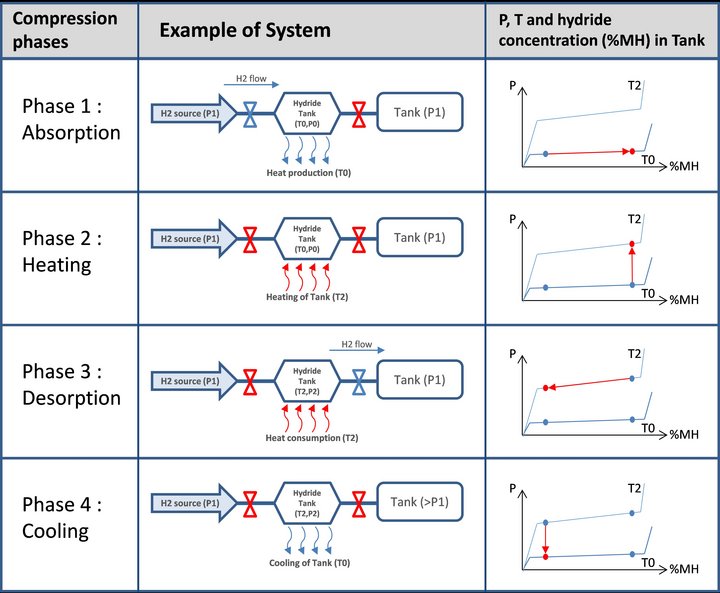
Learn more about
the economic impact of
hydrogen compression
on hydrogen fuel costs
To assure that hydrogen is an attractive fuel also from an economic point of view, hydrogen prices at the pumps need to be in the range of 8 to 10 € per kg of hydrogen. This translates roughly into fuel costs below 8 and 10 € per 100 km driving distance.
Today, the costs for providing hydrogen to the vehicle user are often above this target value. In recent years, innovations and technology development have already achieved significant cost reductions. However, further cost reductions e.g. by applying new and innovative compressor technologies are required. Currently, hydrogen compression at the refuelling station contributes between 1.5 and 2.5 € per kilogram to the total fuel costs. This shows the relevance for further innovation and development.
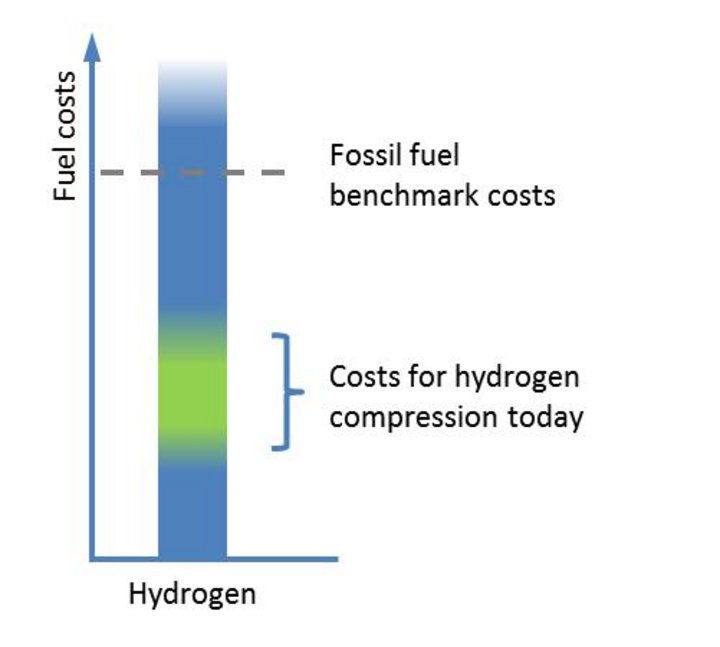